{"source":"\/21005836\/Article_leaderboard_billboard","sizes":"[[728, 90], [320, 50], [300,50]]","adContainerId":"gpt-ad-2013000059"}
Vlaanderen heeft tien nieuwe Fabrieken van de Toekomst
05/03/2019 OM 08:26
- Luc Willemijns
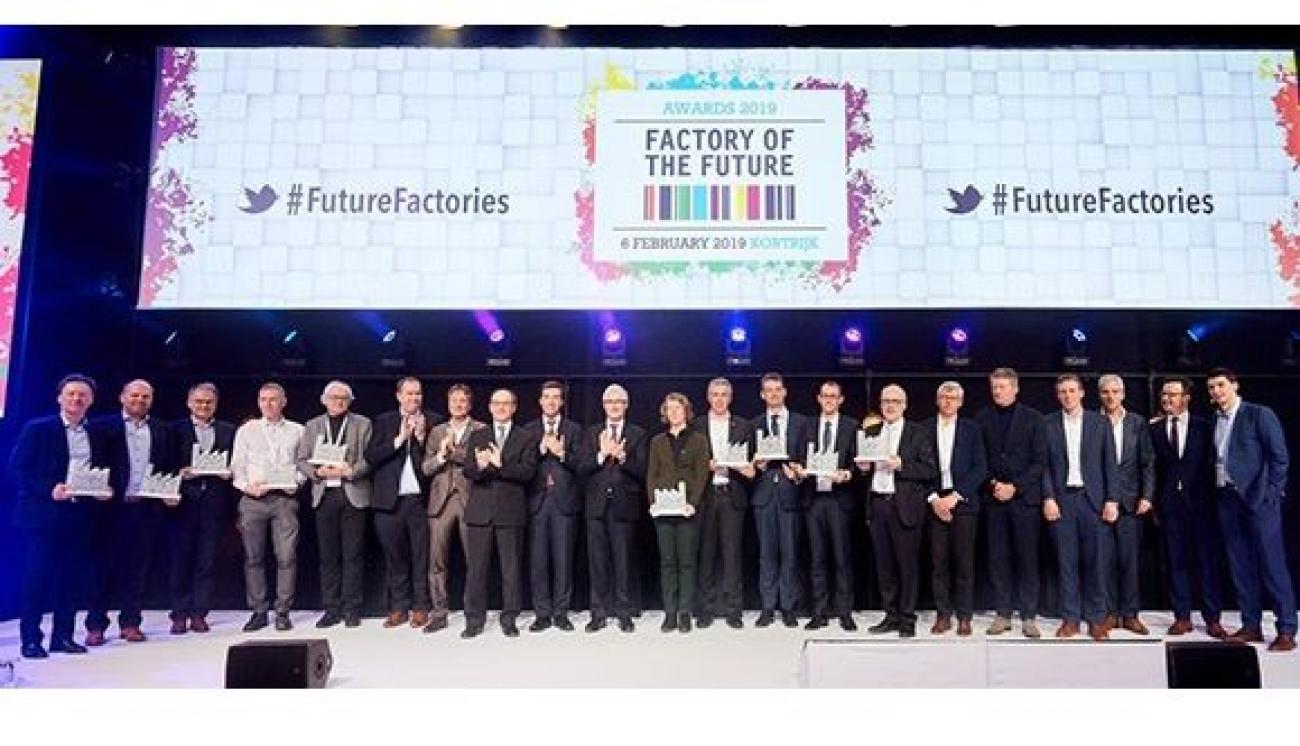
Agoria en Sirris hebben in Kortrijk Expo tijdens de vijfde editie van de “Factory of the Future Awards” nog eens tien maakbedrijven gelauwerd. Laureaten waren BMT Aerospace (Oostkamp), Bosch (Tienen), Colruyt Group Fine Food (Halle), Duracell (Aarschot), Janssen (Geel), Lavetan (Turnhout), Mirion Technologies (Olen), Niko Group (Sint-Niklaas), Materialise (Leuven) en RF-technologies (Oosterzele). Vijf laureaten van 2016 wisten hun status van “Factory of the Future) voor een periode van drie jaar te herbevestigen. Het gaat om Van Hoecke (Sint-Niklaas), Ontex (Erembodegem), ED&A (Kapellen), TE Connectivity (Oostkamp) en Bio Bakkerij De Trog (Ieper).
Ontvang Leads voor 19€/mnd
- Ontvang automatisch info over leads, klanten, concurrenten en partners
- Alle data en artikels staat voor u beschikbaar
- Maandelijks opzegbaar
Wilt u meer bedrijven bereiken?
Word dan dVO Reach en promoot uw bedrijfsverhaal bij 50.000 beslissers.
Voor u geselecteerd
{"source":"\/21005836\/Article_Leaderboard","sizes":"[[728, 90], [320, 50], [300, 50]]","adContainerId":"gpt-ad-1942817121"}
Kort de voordelen van een abonnement...
Belangrijk nieuws te delen?
Ontvang Leads voor 19€/mnd
- Ontvang automatisch info over leads, klanten, concurrenten en partners
- Alle data en artikels staat voor u beschikbaar
- Maandelijks opzegbaar
Wilt u meer bedrijven bereiken?
Word dan dVO Reach en promoot uw bedrijfsverhaal bij 50.000 beslissers.